基于無(wú)人值守的鉻鐵密閉電爐爐頂布料控制系統(tǒng)
隨著不銹鋼工業(yè)的迅速崛起和不銹鋼應(yīng)用領(lǐng)域的擴(kuò)大,從而使得不銹鋼的產(chǎn)量劇增,高碳鉻鐵做為生產(chǎn)不銹鋼所用鉻的主要來(lái)源,可改變鋼的特性,提高鋼的韌性、耐磨性和防腐性,其需求量也隨之急劇增加。為了適應(yīng)市場(chǎng)需要和降低生產(chǎn)成本,現(xiàn)階段生產(chǎn)高碳鉻鐵的大型礦熱電爐,開發(fā)出了預(yù)處理工藝技術(shù),將高溫含鉻預(yù)還原球團(tuán)與硅石、焦炭、回爐渣按照一定工藝配比,直接送入密閉電爐進(jìn)行冶煉鉻鐵,這種工藝的特點(diǎn)就是電耗低、省焦炭、鉻回收率高,大大降低生產(chǎn)成本。采用這種工藝技術(shù)的密閉電爐冶煉鉻鐵的生產(chǎn)過(guò)程中,會(huì)產(chǎn)生C0有毒氣體通過(guò)爐頂加料管排放出來(lái),同時(shí)爐頂配料所加裝預(yù)還原球團(tuán)達(dá)到1 200℃的高溫,這樣的環(huán)境條件對(duì)人來(lái)說(shuō)具有很大的危險(xiǎn)性,為此就需要設(shè)計(jì)無(wú)人值守的配料及爐頂布料控制系統(tǒng),降低事故發(fā)生概率,通過(guò)自動(dòng)控制系統(tǒng),提高鉻鐵產(chǎn)品質(zhì)量。
本文引用地址:http://2s4d.com/article/201610/306662.htm1 工藝流程簡(jiǎn)述
布料系統(tǒng)工藝流程如圖1所示,當(dāng)電爐爐頂某個(gè)或某幾個(gè)供料倉(cāng)發(fā)出求料信號(hào)時(shí),控制系統(tǒng)根據(jù)各缺料料倉(cāng)的料位高度,進(jìn)行缺料程度優(yōu)先級(jí)排序,然后控制軌道罐車啟動(dòng)一次布料流程,按照混合冷料和熱料球團(tuán)的工藝配比值,自動(dòng)移動(dòng)到混合冷料倉(cāng)下,通過(guò)給料皮帶進(jìn)行給料,地磅進(jìn)行稱量,達(dá)到設(shè)定值后自動(dòng)停止給料,然后再移動(dòng)到預(yù)還原熱料球團(tuán)倉(cāng)下,通過(guò)振動(dòng)篩進(jìn)行給料,達(dá)到設(shè)定值后停止給料,關(guān)閉軌道罐車的上口插板,軌道掛車移動(dòng)到優(yōu)先級(jí)較高的求料供料倉(cāng),打開供料倉(cāng)口電動(dòng)插板,再打開罐車下口插板,將混合料流入該爐頂供料倉(cāng),然后關(guān)閉罐車下口插板,關(guān)閉供料倉(cāng)口插板,至此完成一批料的布料過(guò)程。然后控制系統(tǒng)根據(jù)缺料優(yōu)先級(jí)順序,控制軌道罐車進(jìn)行下一批料的布料過(guò)程。整個(gè)過(guò)程從定位、裝料、再到放料完全無(wú)人值守。
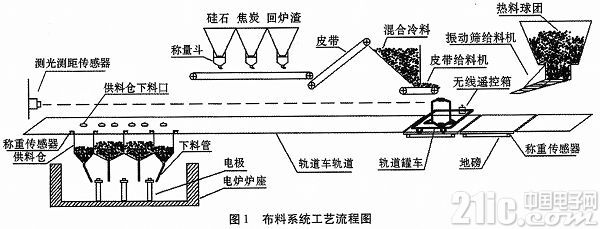
2 系統(tǒng)總體設(shè)計(jì)
依據(jù)現(xiàn)場(chǎng)需要無(wú)人值守的整體工藝特點(diǎn),系統(tǒng)總體采用三層結(jié)構(gòu),管理層由管理計(jì)算機(jī)、工程師站和數(shù)據(jù)服務(wù)器組成:控制層由PLC核心控制單元、數(shù)據(jù)采集單元和無(wú)線數(shù)傳模塊構(gòu)成:執(zhí)行層由各信號(hào)采集變送設(shè)備和動(dòng)作執(zhí)行電機(jī)組成。系統(tǒng)總體構(gòu)架如圖2所示。
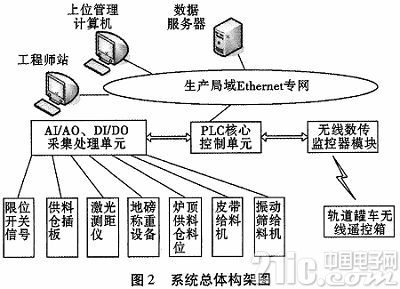
2.1 系統(tǒng)方案配置
2.1.1 軌道罐車定位
系統(tǒng)控制的關(guān)鍵環(huán)節(jié)之一就是讓軌道罐車在給料設(shè)備位置、爐頂供料倉(cāng)下料口位置進(jìn)行準(zhǔn)確定位,隨著激光測(cè)距傳感器技術(shù)的發(fā)展和成本的下降,使得激光在工業(yè)自動(dòng)距離位移測(cè)量和位置控制領(lǐng)域有了廣泛的應(yīng)用,本系統(tǒng)設(shè)計(jì)采用工業(yè)激光測(cè)距傳感器,通過(guò)測(cè)距的方式對(duì)罐車走行進(jìn)行準(zhǔn)確定位,而且可以獲得軌道罐車連續(xù)位置變化。
2.1.2 軌道罐車遙控
隨著元線技術(shù)的發(fā)展,在工業(yè)控制領(lǐng)域開始廣泛的應(yīng)用,鑒于本系統(tǒng)軌道罐車是移動(dòng)的設(shè)備,而且軌道車上的電動(dòng)設(shè)備(走行控制變頻器、插板電液推桿、電力液壓推動(dòng)器剎車裝置)需要和地面PLC控制站進(jìn)行數(shù)據(jù)傳輸和控制,在這種場(chǎng)合下,使用有線電纜進(jìn)行信號(hào)傳輸和控制受到了很大的制約,施工布線麻煩。為此系統(tǒng)設(shè)計(jì)對(duì)罐車的走行、料罐上下口插板的控制選用無(wú)線數(shù)傳控制技術(shù),通過(guò)無(wú)線數(shù)傳設(shè)備,完成模擬量信號(hào)和數(shù)字量信號(hào)的雙向傳輸。
2.1.3 速度控制
為了確保配料過(guò)程中料種的配比精度,就需要對(duì)給料設(shè)備的慣性沖量進(jìn)行嚴(yán)格控制,使各料種稱量值之間的比例最大限度的接近工藝配比,為此系統(tǒng)對(duì)給料裝置給料速度采用了變頻速度調(diào)節(jié),通過(guò)程序軟件建立速度控制方法的數(shù)學(xué)模型,對(duì)給料速度按照模型曲線進(jìn)行無(wú)極連續(xù)變化控制,既兼顧了配料效率,也使得慣性沖量對(duì)配比的影響降到最小程度。同樣,對(duì)軌道車的走行控制也采用了類似的變頻控制手法,可以提高軌道車的走行效率和平穩(wěn)性。
2.1.4 PLC控制核心
依據(jù)整體工藝特點(diǎn),計(jì)算機(jī)控制系統(tǒng)設(shè)計(jì)采用西門子S7-300系列PLC為系統(tǒng)控制的核心,配置以太網(wǎng)通信模塊、模擬量輸入/輸出模塊、開關(guān)量輸入/輸出模塊,接收來(lái)自上位管理計(jì)算機(jī)的控制指令和生產(chǎn)任務(wù)計(jì)劃指令,并將所控制設(shè)備的開關(guān)狀態(tài)和模擬數(shù)值量上傳給管理層計(jì)算機(jī),進(jìn)行數(shù)據(jù)分析和統(tǒng)計(jì)。采集爐頂供料倉(cāng)的重量信息獲得料倉(cāng)求料信號(hào),再通過(guò)無(wú)線數(shù)傳遙控方式,采集軌道罐車的走行速度,進(jìn)而控制軌道車的走行和上下口插板的開合;采集激光測(cè)距傳感器的距離信號(hào),對(duì)軌道罐車進(jìn)行準(zhǔn)確的定位;采集地磅的稱重信號(hào)和給料設(shè)備的速度信號(hào),以上各模擬量信號(hào)通過(guò)4 mA~20 mA傳輸給PLC,供PLC控制軟件分析計(jì)算,根據(jù)控制要求,經(jīng)過(guò)控制軟件智能調(diào)節(jié)器的運(yùn)算及數(shù)據(jù)處理,給出速度模擬量調(diào)節(jié)信號(hào),完成自動(dòng)給料及稱量,通過(guò)PLC利用現(xiàn)代控制理論,自動(dòng)完成生產(chǎn)過(guò)程關(guān)聯(lián)集控設(shè)備的控制和調(diào)節(jié)。
2.1.5 上位管理軟件
遠(yuǎn)程管理計(jì)算機(jī)采用intouch工業(yè)自動(dòng)化組態(tài)軟件,完成對(duì)生產(chǎn)任務(wù)的編排,生產(chǎn)過(guò)程的顯示、控制、操作和管理,對(duì)配料和布料數(shù)據(jù)進(jìn)行統(tǒng)計(jì)分析,產(chǎn)生統(tǒng)計(jì)報(bào)表和數(shù)據(jù)動(dòng)態(tài)曲線。以直觀動(dòng)態(tài)的方式真實(shí)反映生產(chǎn)現(xiàn)場(chǎng)各設(shè)備的位置、動(dòng)作情況、計(jì)劃執(zhí)行情況、故障報(bào)警信息,同時(shí)信息數(shù)據(jù)接入生產(chǎn)局域?qū)>W(wǎng),實(shí)現(xiàn)系統(tǒng)數(shù)據(jù)共享和上層監(jiān)督,管理功能框圖如圖3所示意。

2.2 關(guān)鍵支撐技術(shù)
2.2.1 激光測(cè)距定位
激光測(cè)距是光波測(cè)距中的一種測(cè)距方式,如果光以速度c在空氣中傳播在A、B兩點(diǎn)間往返一次所需時(shí)間為t,則A、B兩點(diǎn)間距離D可用下列表示。
D=ct/2
式中:D-測(cè)站點(diǎn)A、B兩點(diǎn)間距離;
c-光在大氣中傳播的速度;
t-光往返A(chǔ)、B一次所需的時(shí)間。
由上式可知,要測(cè)量A、B距離實(shí)際上是要測(cè)量光傳播的時(shí)間t,根據(jù)測(cè)量時(shí)間方法的不同,激光測(cè)距儀通??煞譃槊}沖式和相位式兩種測(cè)量形式。相位式激光測(cè)距精度高,但為了有效的反射信號(hào),需要配置反射鏡,并使測(cè)定的目標(biāo)限制在與儀器精度相稱的某一特定點(diǎn)上,在工業(yè)現(xiàn)場(chǎng)的使用具有一定的局限性。
基于本系統(tǒng)是對(duì)工業(yè)現(xiàn)場(chǎng)直線移動(dòng)軌道車定位,選用SENST系列一維工業(yè)激光位移傳感器,利用紅色激光瞄準(zhǔn)方式,動(dòng)態(tài)的對(duì)移動(dòng)物體的相對(duì)距離進(jìn)行測(cè)量,通過(guò)采用數(shù)字測(cè)相脈沖展寬細(xì)分技術(shù),無(wú)需合作目標(biāo)即可達(dá)到毫米級(jí)精度,測(cè)程已經(jīng)超過(guò)100 m。本系統(tǒng)設(shè)計(jì)選用量程為0.2 m~70 m的激光測(cè)距傳感器,測(cè)量精度達(dá)±2 mm,分辨率0.1 mm,測(cè)量結(jié)果以4 mA~20 mA方式傳輸PLC用于計(jì)算和控制,完全滿足使用要求。
2.2.2 無(wú)線數(shù)傳控制
無(wú)線數(shù)傳模塊是數(shù)傳電臺(tái)的模塊化產(chǎn)品,借助DSP技術(shù)和無(wú)線電技術(shù)實(shí)現(xiàn)高性能專業(yè)數(shù)據(jù)傳輸,具有數(shù)字信號(hào)處理、數(shù)字調(diào)制解調(diào)、數(shù)據(jù)前向糾錯(cuò)、均衡軟判決等功能??梢詫⒐I(yè)現(xiàn)場(chǎng)設(shè)備輸出的數(shù)據(jù)(模擬量和開關(guān)量)進(jìn)行遠(yuǎn)程無(wú)線傳輸和控制。本系統(tǒng)設(shè)計(jì)選用的無(wú)線數(shù)傳模塊采用中國(guó)新開通的780 M頻段,避免了2.4 GHz和433 MHz頻段內(nèi)民用無(wú)線設(shè)備的干擾,與其他ISM頻段無(wú)線收發(fā)器相比,具有低功耗、高靈敏度和穿透力強(qiáng)、通信質(zhì)量更好等特點(diǎn)。
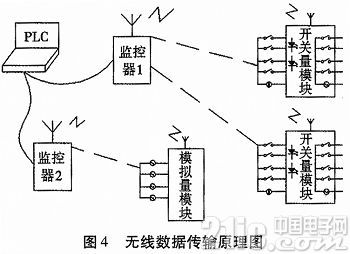
本系統(tǒng)通過(guò)PLC連接無(wú)線監(jiān)控器的方式,遠(yuǎn)程管理多個(gè)無(wú)線開關(guān)量控制器和模擬量控制器,數(shù)據(jù)傳輸原理如圖4所示。采用GFSK的調(diào)制方式;收發(fā)一體,半雙工,數(shù)據(jù)收發(fā)轉(zhuǎn)換自動(dòng)完成;信道速率選用19 200 bps;接口方式為RS-485;發(fā)射功率100 MW;工作溫度-40 ℃~+85 ℃。動(dòng)作過(guò)程:當(dāng)遠(yuǎn)程無(wú)線控制器的輸入通道數(shù)據(jù)信號(hào)發(fā)生改變時(shí),發(fā)送報(bào)告到監(jiān)控器,監(jiān)控器更新相關(guān)的映像寄存器或狀態(tài),PLC讀取這些寄存器或狀態(tài)。PLC可以通過(guò)寫寄存器或狀態(tài)的方式,直接控制遠(yuǎn)程設(shè)備的輸出狀態(tài)。
3 系統(tǒng)軟件
3.1 系統(tǒng)控制算法分析
系統(tǒng)的配料和布料過(guò)程是將混合冷料和高溫預(yù)還原熱料球團(tuán)按照工藝配比分批稱量后,向電爐爐頂供料倉(cāng)內(nèi)投料,屬于典型的間歇工作模式,對(duì)于皮帶給料和振動(dòng)篩給料,由于慣性沖量的存在,無(wú)法做到每批料按照設(shè)定值進(jìn)行準(zhǔn)確的稱量,必然存在稱量值與設(shè)定值的偏差,為了彌補(bǔ)這種離散偏差對(duì)整體物料配比工藝的影響,為此在控制軟件上引入了基于速度調(diào)節(jié)控制的稱量數(shù)學(xué)模型,提高單批配料過(guò)程的稱量精度和效率,同時(shí)采用后批重量補(bǔ)償前批重量的算法,通過(guò)歷史數(shù)據(jù)優(yōu)化給定,來(lái)矯正每批料稱量值的離散偏差,使多批料的總體配比最大限度的接近于工藝設(shè)定配比值。
主要控制算法用近似語(yǔ)言描述如下,分號(hào)后為注釋:
p(n-1)=c(n-1)-s(n-1); 計(jì)算上次配料偏差
s(n)=Q-p(n-1) ; 計(jì)算本次給料的控制給定值
其中p表示偏差,c表示實(shí)際稱量值,s表示控制給定值(隨動(dòng)變量),Q表示給定值(常量),n是一個(gè)時(shí)間標(biāo)量,具體含義是n-1表示前一次,n表示本次??紤]到給料機(jī)有慣性沖量存在的因素,在控制給料停止的過(guò)程中,設(shè)置一個(gè)沖量預(yù)補(bǔ)提前量,來(lái)補(bǔ)償給料機(jī)停止后物料的慣性沖量,同時(shí)依賴歷史數(shù)據(jù),構(gòu)造一個(gè)算法,使之每次產(chǎn)生一個(gè)新值,來(lái)盡量的縮小每批料稱量值與控制給定值之間的偏差。
3. 2 變頻速度調(diào)節(jié)控制數(shù)學(xué)模型的建立
3.2.1 給料速度控制方法
間歇式分批配料過(guò)程,不僅要控制稱量的精度,而且要控制配料的速度,實(shí)現(xiàn)高精度、快速稱量是該系統(tǒng)的關(guān)鍵技術(shù)之一,在傳統(tǒng)的雙速給料中,給料裝置振動(dòng)力大或速度快則給料快,但精度難以控制,振動(dòng)力小或速度慢則給料慢,精度可以保證,但稱量時(shí)間長(zhǎng),效率低,由于本系統(tǒng)的給料裝置屬于非線性,采用雙速給料不是理想的控制方式,為此提出了給料速度控制的方法,如圖5所示,采用閉環(huán)控制,以給料速度為控制參數(shù),根據(jù)稱量重量控制給料速度,兼顧效率和精度。在稱量初期,給料速度穩(wěn)定在V0,是一個(gè)定值調(diào)節(jié)系統(tǒng),當(dāng)稱量值接近設(shè)定值時(shí),速度的趨于逐漸減小,從而變?yōu)殡S動(dòng)調(diào)節(jié)系統(tǒng),將傳統(tǒng)的分段速度控制改為無(wú)極連續(xù)調(diào)節(jié)。
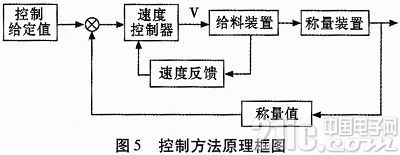
3.2.2 給料速度調(diào)節(jié)控制數(shù)學(xué)模型
在皮帶給料和振動(dòng)給料過(guò)程中,根據(jù)稱量控制設(shè)定值,在指定的時(shí)間內(nèi)完成物料稱量,此稱量物料過(guò)程是對(duì)物料重量的累積關(guān)系。設(shè)W為物料的稱量值(單位:kg),V為給料速度(單位:kg/s),T為給料時(shí)間(單位:s),則有以下積分關(guān)系:

式中,W’為單位時(shí)間的稱料量
設(shè)物料的控制稱量設(shè)定值為Ws,在0到t1時(shí)間段,以恒定V0速度給料,到達(dá)t1時(shí),物料稱量值W距設(shè)定值Ws的差量為Wx,此后稱量速度V開始隨著稱量值的增大逐漸降低,直至趨于零。設(shè)
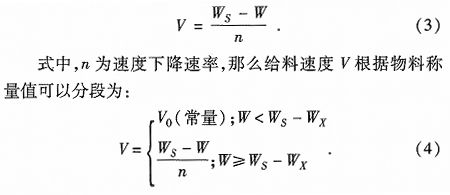
當(dāng)物料下料累計(jì)稱量值W未達(dá)到時(shí)WS-WX,給料速度為定值調(diào)節(jié),當(dāng)物料累計(jì)稱量值大于WS-WX,速度控制為隨動(dòng)調(diào)節(jié)。對(duì)于恒速調(diào)節(jié)階段,易于實(shí)現(xiàn),對(duì)于變速調(diào)節(jié)階段,由(2)、(3)和(4)式推導(dǎo)得出:
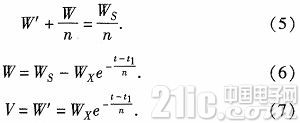
根據(jù)速度可以畫出物料稱量值W、給料速度V和稱量時(shí)間t的關(guān)系曲線如圖6所示。實(shí)際應(yīng)用中,根據(jù)物料的特性,選擇適當(dāng)?shù)腤X和η值,既可以保證稱量精度,也可以兼顧稱量速度,具有較強(qiáng)的靈活性和適應(yīng)性。
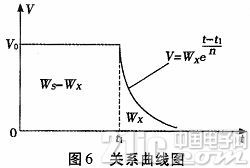
4 系統(tǒng)運(yùn)行及調(diào)試
經(jīng)過(guò)前期的設(shè)計(jì)、開發(fā)和調(diào)試,最終將系統(tǒng)整體應(yīng)用到實(shí)際現(xiàn)場(chǎng)中,通過(guò)測(cè)試及功能完善,從軌道車自動(dòng)定位、給料裝置自動(dòng)給料、地磅自動(dòng)稱量、軌道車自動(dòng)走行及放料,整體過(guò)程動(dòng)作連續(xù),嚴(yán)格按照工藝要求執(zhí)行,PLC控制軟件根據(jù)系統(tǒng)控制算法,對(duì)配料過(guò)程自動(dòng)修正和補(bǔ)償,取得了比較理想的配比工藝曲線,上位機(jī)軟件也能夠?qū)崟r(shí)、快速地將現(xiàn)場(chǎng)采集的數(shù)據(jù)結(jié)果顯示給操作人員,并進(jìn)行曲線生成和數(shù)據(jù)統(tǒng)計(jì)分析。
5 結(jié)束語(yǔ)
系統(tǒng)綜合了工業(yè)測(cè)控技術(shù)、無(wú)線數(shù)傳控制技術(shù)和現(xiàn)代軟件技術(shù),使整體系統(tǒng)具有良好的智能性、擴(kuò)展性,通過(guò)無(wú)人值守控制系統(tǒng),實(shí)現(xiàn)地面對(duì)遠(yuǎn)程設(shè)備的監(jiān)控指揮,大大提高了企業(yè)生產(chǎn)過(guò)程的簡(jiǎn)潔性和日常維護(hù)效率。
評(píng)論