機器視覺在汽車制造業(yè)中的應(yīng)用
“機器視覺”的用途很多,隨著20世紀(jì)90年代以來光電、自動化和計算機圖像處理技術(shù)的迅速發(fā)展,機器視覺已在包括汽車制造業(yè)在內(nèi)的很多工業(yè)部門得到越來越廣泛的應(yīng)用。作為一種新穎而又實用的傳感技術(shù),圖像檢測單元近年已實現(xiàn)產(chǎn)品化,一些知名的廠商,如日本的松下公司、德國的西門子公司等都推出了品種規(guī)格齊全的系列化產(chǎn)品,包括光源、攝像頭、處理器等,對圖像檢測技術(shù)的推廣應(yīng)用創(chuàng)造了有利的條件。與此同時,所頒布的相關(guān)標(biāo)準(zhǔn)不但規(guī)范了生產(chǎn),而且為用戶在不同情形下選用合適的檢測單元,更快、更好地進行系統(tǒng)設(shè)計提供了依據(jù)。
本文引用地址:http://2s4d.com/article/196635.htm相比之下,國內(nèi)在這方面尚處于起步階段,即使在近20年獲得迅速發(fā)展的汽車制造業(yè),機器視覺的應(yīng)用也相當(dāng)有限。但通過以下應(yīng)用實例,可清楚地看出這項新技術(shù)的應(yīng)用前景。
在精密測量中的應(yīng)用
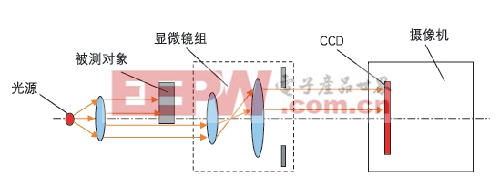
圖1 位移檢測系統(tǒng)示意圖
精密測量是機器視覺一個重要的應(yīng)用領(lǐng)域,其對被測對象進行測量的原理如圖1所示。檢測系統(tǒng)主要由光學(xué)系統(tǒng)、CCD攝像頭和計算機處理系統(tǒng)(圖中未表示)等組成。由光源發(fā)出的平行光束照射到被測對象的檢測部位上,其邊緣輪廓經(jīng)過顯微光學(xué)鏡組成像在攝像機的面陣CCD像面上,經(jīng)計算機進行圖像處理后獲得被測對象邊緣輪廓的位置。如果使被測對象產(chǎn)生位移,再次測量其邊緣輪廓位置,則兩次位置之差便是位移量。顯然,若被測對象的兩條平行的邊緣輪廓能處于同一幅圖像內(nèi),則其二者位置之差即為相應(yīng)尺寸。
上述系統(tǒng)極為適合對大批量生產(chǎn)情況下工件的在線檢測,尤其是當(dāng)被測對象尺寸較小、形狀比較簡單時,更能顯示其優(yōu)越性。電子接插件,包括汽車電子產(chǎn)品中的接插件就是典型例子,它們的生產(chǎn)效率和成品尺寸精度都較高,前者可達到每分鐘數(shù)百件,而后者多數(shù)為0.01mm的數(shù)量級。當(dāng)采用圖1所示系統(tǒng)進行測量時,零件(插腳)所形成的圖像由于與其明亮背景之間的強烈對比,而具有清晰的剪影效果。這樣的理想圖像為準(zhǔn)確測量被檢對象的尺寸和輪廓(形狀)特征創(chuàng)造了條件。圖2顯示了一部分沖壓成形的插腳隨著金屬輸送帶通過檢測工位時產(chǎn)生的典型背光圖像。
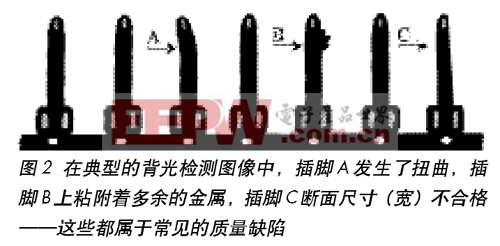
需指出的一點是,盡管采用的是對零件圖像的邊緣檢測,但根據(jù)工件的不同情況,具體做法上仍有差別。如對圖2所示零件(插腳)的圖像上可以設(shè)置3條(L1、L2、L3)或多條檢測線,分別采用簡單的閥值法或單雙峰法檢測出零件的邊緣信息。由于3條檢測線之間保持著相互垂直交叉的關(guān)系,因此可以通過聯(lián)立3線(或多線)的邊緣檢測點確定插腳相對于圖像平面的位置(X、Y)和轉(zhuǎn)角(?)。這些目標(biāo)零件的位置信息(邊緣坐標(biāo)和起始轉(zhuǎn)角)將傳送給計算機處理系統(tǒng),以做出相應(yīng)的評價。
圖像檢測技術(shù)用于精密測量的另一個實例是在刀具預(yù)調(diào)測量中的應(yīng)用。傳統(tǒng)的檢測方式是光學(xué)投影和光柵數(shù)顯表相結(jié)合,前者用于瞄準(zhǔn)定位,后者用于測量、讀數(shù)。整個過程需較多的人工參與,對操作人員的要求高,效率卻較低。幾年前誕生的新穎刀具預(yù)調(diào)測量儀把機器視覺、光柵技術(shù)、計算機軟硬件、自動控制技術(shù)等有機結(jié)合,使傳統(tǒng)的工作方式發(fā)生了根本變化,無論在測量精度、操作方便和工作效率上都有了極大的提高。而主要原因就是以機器視覺替代了傳統(tǒng)的光學(xué)投影,從而徹底改變了原有的工作模式。
在這種新穎儀器中,作為運動導(dǎo)軌的Z軸、X軸和C(回轉(zhuǎn))軸內(nèi),分別裝有直線光柵和圓光柵,被測刀具沿轉(zhuǎn)臺中心線(即C軸)0安裝。機器視覺傳感器位于叉形支架兩側(cè),也就是跨越轉(zhuǎn)臺的中心線。支架的一端安放光源,而另一端是攝像頭,被測刀具的圖像由攝像頭讀取。
對工件表面缺陷的檢測
對表面缺陷的探測在批量生產(chǎn)的汽車、摩托車、內(nèi)燃機等行業(yè),迄今基本都采用人工目測方法。這樣的方法不但效率低、勞動強度大,且對工藝標(biāo)準(zhǔn)中規(guī)定的定量評定要求往往難以準(zhǔn)確執(zhí)行,從而影響對產(chǎn)品質(zhì)量的有效監(jiān)控。
.
以連桿結(jié)合面爆口為例,其評定標(biāo)準(zhǔn)的具體要求是:破口面積小于3mm2;破口任一方向的線性長度小于2.5mm。只要符合上述任一條件,就將判定不合格而被剔除。
必須指出,與以上精密測量中機器視覺系統(tǒng)采用的透射方式(又稱“背光” 方式)不同,用于表面缺陷探測時,需采取圖3所示的反射方式。
該系統(tǒng)通過一個方形框式LED漫反射光源照亮待檢測工件的破口區(qū)域,光線照射到對象表面后,反射到攝像頭內(nèi)的光電耦合CCD元件上,即轉(zhuǎn)化成對應(yīng)的電量信號;圖像處理系統(tǒng)根據(jù)電量信號對得到的圖像進行分析和計算,最終得到所需的數(shù)據(jù)。系統(tǒng)將得到的圖像進行二值化處理后,把二值圖像作為對象進行進一步的計算分析。
在實際使用中,該系統(tǒng)對于灰度的二值化閾值和光源的設(shè)定采用比對的方法實現(xiàn),即用已知的樣件作為標(biāo)定的參照物。把已知的參照物測量
值除以參照物對應(yīng)的像素值,即可得到像素與實際值之間的對應(yīng)比例值。通過調(diào)整光源亮度以及系統(tǒng)的二值化閾值,對灰度的二值化閾值進行優(yōu)化,保證系統(tǒng)對對象邊界具有相對較高的分辨率,即優(yōu)化后的二值化閾值和光源可以使邊界的變化產(chǎn)生盡量大的像素值變化。
根據(jù)被測對象的特征(工件形狀、被測部位)和要求,參照視覺系統(tǒng)產(chǎn)品的有關(guān)標(biāo)準(zhǔn),并按照所完成的設(shè)計,將能方便地選取合適的圖像檢測單元(器件),組成相應(yīng)的檢測系統(tǒng)。以連桿結(jié)合面爆口為例,其系統(tǒng)的檢測要求如圖4所示,即分別檢測互為15。夾角的A-B-C三個(連桿側(cè)面的)破口面,最終以3個檢測結(jié)果中的最大值作為破口的真實值,進行判斷后并輸出結(jié)果。圖5為該系統(tǒng)組成示意圖,其中:
1. CD攝像頭用于采集破口圖像并轉(zhuǎn)換成數(shù)字圖像信號;
2. LED光源用于提供穩(wěn)定的、均勻的照明,保證取像質(zhì)量;
3.圖像處理單元的用途是根據(jù)需要對采集到的圖像進行處理、分析,同時把分析結(jié)果和圖像系統(tǒng)的狀態(tài)信息通過RS232接口傳向PLC提供信號輸出和數(shù)據(jù)交換;
4.PLC控制整個檢測系統(tǒng)各項功能的執(zhí)行,同時也對圖像處理單元傳過來的數(shù)據(jù)進行校驗和判斷;
5. 監(jiān)示器作為人機交互界面,顯示圖像處理系統(tǒng)的狀態(tài)和數(shù)據(jù)分析結(jié)果。
用于圖像識別的機器視覺系統(tǒng)的檢測原理雖然與以上表面缺陷探測相似,但作用、目的完全不同。且相比之下,即使在國內(nèi)汽車制造業(yè)中的應(yīng)用也較前兩個領(lǐng)域為多。
.
現(xiàn)代工業(yè)則已越來越多地采取讓最終產(chǎn)品、甚至半成品(零部件)帶有用于識別的一維、二維條碼。在大批量生產(chǎn)條件下,如何對它們識別、判斷?若依靠人工肉眼檢查,不但勞動強度大,也難免錯檢漏判。另一方面,在生產(chǎn)線、特別是其中那些裝配工序的運行中,為正確完成規(guī)定的要求,往往也需解讀一維、二維條碼或識別某些印刷字體;此外,很多情況下,對零件的姿態(tài)、位置(方向)也必須進行辨識,特別在采用選擇裝配方式時。電子標(biāo)簽也是近年發(fā)展起來的一項新技術(shù),它采用機器視覺的識別技術(shù),將涉及發(fā)動機的各種質(zhì)量信息通過讀寫器無線寫入標(biāo)簽或讀出。在有些發(fā)動機生產(chǎn)線的輸送裝置(托盤)上安裝有一個電子標(biāo)簽,而每個加工或裝配工位則布置有一個讀寫器。讀寫器與PLC或計算機相連。
1. 活塞在缸體內(nèi)的裝配
圖像識別技術(shù)在用于“活塞—缸體裝配工序”時,其主要環(huán)節(jié)包括:判斷缸體到位并做好檢測準(zhǔn)備;探測缸體上緣(準(zhǔn)確到位的標(biāo)志),如果未發(fā)現(xiàn)該特征部分,即發(fā)出報警信號;在檢測系統(tǒng)中建立坐標(biāo)系;識別這樣三項內(nèi)容:活塞的有無,活塞位置的正確性(確切地講
是“方位”),活塞頂部表面的標(biāo)識和字符——用于表明型號、選擇裝配時的組別及其他相關(guān)含義。
整個檢測、識別過程如下:發(fā)動機被翻轉(zhuǎn)、裝入活塞,輸送系統(tǒng)使發(fā)動機隨托盤向檢測工位移動;當(dāng)發(fā)動機即將到達檢測工位時,由電子標(biāo)簽讀寫器驗明其“身份”,然后發(fā)信號給PLC;而當(dāng)發(fā)動機到達檢測工位,接近開關(guān)觸發(fā),PLC給機器視覺系統(tǒng)發(fā)出工作指令;如果活塞在缸體內(nèi)的裝配正確,視覺系統(tǒng)發(fā)信給PLC,然后寫入電子標(biāo)簽,發(fā)動機繼續(xù)流向下一工位。如果活塞裝配有錯,則視覺系統(tǒng)提示PLC,并通過人機界面報警,顯示屏將指示哪一缸的活塞裝配有錯、何種錯誤。操作者確認檢測結(jié)果后,通過使人機界面PLC發(fā)出指令將結(jié)果寫入電子標(biāo)簽,并且將發(fā)動機直接輸送到返修區(qū)域進行返修。整個檢測過程全部自動完成,只是在出現(xiàn)裝配錯誤、發(fā)出報警時才由人工干預(yù)。
2.主軸承蓋在缸體上的裝配
在四缸發(fā)動機的缸體生產(chǎn)線,主軸承蓋在缸體上的裝配是又一個典型示例。5個主軸承蓋的前端部呈不同的臺階狀,各不相同。通過每個零件上的數(shù)字標(biāo)識,按規(guī)定順序和方向安裝。由于零件混雜、數(shù)量又大,常發(fā)生錯裝現(xiàn)象,導(dǎo)致下道工序產(chǎn)生廢品。
為此,在生產(chǎn)線的擰緊裝配工位和翻轉(zhuǎn)工位之間設(shè)置一檢測工位,通過自動識別,判斷裝配結(jié)果的正確性。若全部正確,則缸體繼續(xù)流向下一工位,否則報警并給PLC發(fā)出指令,使生產(chǎn)線停機,將有問題的缸體下線返修。為了適應(yīng)1件/min的裝配節(jié)拍,采用在缸體移動過程中檢測,2個光電視覺傳感器分別前后布置在生產(chǎn)線的上方和一側(cè)。前一個為零件定位傳感器,用以自動準(zhǔn)確地觸發(fā)采樣,后一個用于動態(tài)識別5個主軸承蓋的表面幾何形狀。根據(jù)預(yù)先置入的各主軸承蓋特征參數(shù)和采集到的傳感器輸出信號,可確定是否裝錯并指示具體出錯位置。
整個檢測、識別過程為:缸體在完成主軸承蓋的擰緊工序后,沿輥道向檢測工位移動,而兩側(cè)導(dǎo)軌的約束作用,保證了零件自動找正位置。當(dāng)進入檢測工位時,定位傳感器首先探測到第1主軸承蓋邊緣,隨即由另一個傳感器識別其前端部的幾何形狀,經(jīng)控制器采樣、處理;然后缸體繼續(xù)前移,對第2至第5個主軸承蓋進行探測和識別。通過與預(yù)置值比較,就可對有否錯裝零件做出判斷。每次探測都有計數(shù)和顯示,整個檢測過程在缸體輸送移動中完成,不必額外增加檢測時間。
電容式接近開關(guān)相關(guān)文章:電容式接近開關(guān)原理
評論