基于PCI總線的真空差壓鑄造控制設(shè)計(jì)
真空差壓鑄造技術(shù)采用真空條件下低壓充型,高壓結(jié)晶的工藝原理,具有優(yōu)越的充型流 體力學(xué)和凝固力學(xué)條件,在航空航天、國(guó)防和汽車工業(yè)領(lǐng)域的近無(wú)余量、大型、薄壁、復(fù)雜 有色合金鑄造方面顯示了巨大的生命力。而在真空差壓鑄造的過(guò)程中,先進(jìn)的控制技術(shù)是完 成抽真空、充型、升壓、保壓和卸壓等工藝階段的關(guān)鍵環(huán)節(jié),在合理設(shè)計(jì)工藝參數(shù)的基礎(chǔ)上, 對(duì)整個(gè)工藝過(guò)程的準(zhǔn)確控制就成了獲得高質(zhì)量、高成品率鑄件的關(guān)鍵,因此研制先進(jìn)的鑄造 控制系統(tǒng)是保證整個(gè)工藝過(guò)程得以準(zhǔn)確實(shí)施的基礎(chǔ)?;趩纹⑿陀?jì)算機(jī)控制的真空差壓鑄 造控制系統(tǒng)雖然達(dá)到了一定的智能控制要求,并在實(shí)際得到了應(yīng)用,但其還存在以下問(wèn)題: ①所有功能都通過(guò)單片機(jī)來(lái)實(shí)現(xiàn),軟件系統(tǒng)龐大,使單片微型計(jì)算機(jī)運(yùn)行效率下降;②單片 機(jī)難以實(shí)現(xiàn)先進(jìn)控制算法復(fù)雜的程序設(shè)計(jì);③人機(jī)交流停留在傳統(tǒng)的 LED 和按鍵,這樣在工藝參數(shù)設(shè)置和工藝流程運(yùn)行狀況監(jiān)控等方面存在不足;④在實(shí)現(xiàn)工業(yè)以太網(wǎng)監(jiān)測(cè)與控制上 存在一定難度。針對(duì)以上問(wèn)題本課題提出了基于 PCI 總線技術(shù)、面向?qū)ο蟮腃++語(yǔ)言的設(shè) 計(jì)思想,并配以先進(jìn)的壓力傳感器和氣動(dòng)薄膜調(diào)節(jié)閥設(shè)計(jì)一套適用于大型薄壁鋁合金的真空 差壓鑄造智能控制系統(tǒng)。
本文引用地址:http://2s4d.com/article/201612/329526.htm1、系統(tǒng)結(jié)構(gòu)及工作原理
整個(gè)真空差壓鑄造控制系統(tǒng)的硬件由工業(yè)控制計(jì)算機(jī)、基于 PCI 總線高分辨率多功能數(shù)據(jù)采集處理卡PCI-1716、壓力檢測(cè)電路、調(diào)節(jié)閥控制電路、開(kāi)關(guān)信號(hào)檢測(cè)電路、開(kāi)關(guān)閥 驅(qū)動(dòng)電路、和直流穩(wěn)壓電源等部分組成,系統(tǒng)整體框圖如圖1 所示。系統(tǒng)主控計(jì)算機(jī)采用研 華公司高性能工業(yè)控制計(jì)算機(jī)(CPU/P4 2.8G、Windows XP),它是整個(gè)鑄造控制系統(tǒng)的重 要平臺(tái),主要負(fù)責(zé)整個(gè)鑄造控制系統(tǒng)的工藝參數(shù)輸入、運(yùn)行狀態(tài)顯示、數(shù)據(jù)處理與保存以及 對(duì)整個(gè)鑄造過(guò)程的工藝運(yùn)行精確控制。壓力檢測(cè)隔離電路由壓力傳感器、I/V 轉(zhuǎn)換與隔離電 路和PCI-1716 的A/D 轉(zhuǎn)換電路組成。PCI-1716 數(shù)據(jù)采集卡是硬件部分的核心,主要完成模擬量、數(shù)字量數(shù)據(jù)的采集、存儲(chǔ)和輸出。它是研華公司一款功能強(qiáng)大的高分辨率多功能PCI 數(shù)據(jù)采集卡,PCI-1716 可以提供16 路單端模擬量輸入和8 路差分模擬量輸入,也可組合輸 入;它帶有一個(gè)采樣速率最高達(dá)250KS/s 的16 位A/D 轉(zhuǎn)換器;它還帶有2 個(gè)16 位D/A 輸 出通道、16 路數(shù)字量輸入/輸出通道;并附有32 位DLL 驅(qū)動(dòng)程序,通過(guò)這個(gè)驅(qū)動(dòng)程序,編 程人員可以通過(guò)VC++、VB、DELPHI 或C++Builder 等高級(jí)語(yǔ)言編程環(huán)境對(duì)硬件進(jìn)行編程 控制。調(diào)節(jié)閥控制電路由PCI-1716 的D/A 轉(zhuǎn)換電路和V/I 轉(zhuǎn)換及隔離電路組成,它將工控 機(jī)控制軟件計(jì)算的數(shù)字控制量轉(zhuǎn)換成4~20mA 模擬信號(hào)控制氣動(dòng)薄膜調(diào)節(jié)閥的開(kāi)啟度。開(kāi)關(guān) 信號(hào)檢測(cè)電路完成上下鑄罐鎖緊到位、充型到頂和漏液等信號(hào)的檢測(cè),控制軟件利用這些信 號(hào)保證鑄造系統(tǒng)正常、安全、有序的運(yùn)行。開(kāi)關(guān)閥驅(qū)動(dòng)電路利用功率驅(qū)動(dòng)器件將工控機(jī)輸出 的數(shù)字信號(hào)放大成驅(qū)動(dòng)二位三通電磁閥的控制信號(hào),實(shí)現(xiàn)對(duì)氣動(dòng)薄膜開(kāi)關(guān)閥的控制。直流穩(wěn) 壓電源為接口電路和傳感器等提供所需的直流穩(wěn)壓電源。

圖 1 基于PCI 總線的真空差壓鑄造控制系統(tǒng)硬件框圖
2、壓力檢測(cè)與隔離電路
壓力檢測(cè)與隔離電路由壓力傳感器、I/V 轉(zhuǎn)換與隔離電路和PCI-1716 的A/D 轉(zhuǎn)換電路 組成。其中,壓力傳感器檢測(cè)電路測(cè)量上、下鑄罐和上、下儲(chǔ)氣罐共四路壓力值,鑄罐內(nèi)為 絕壓傳感器,儲(chǔ)氣罐內(nèi)為表壓傳感器。壓力傳感器測(cè)量范圍0~1.0MPa,輸出信號(hào)為4~20mA 電流值,電流經(jīng)I/V 隔離轉(zhuǎn)換模塊ISO-A4-P1-O4 轉(zhuǎn)換成與壓力測(cè)量端完全隔離的0~5V 電 壓信號(hào),經(jīng)PCI-1716 的16 位高分辨率A/D 模塊轉(zhuǎn)成數(shù)字量被控制軟件采集,控制軟件的 壓力測(cè)量分辨率可達(dá)15.0Pa??刂栖浖鶕?jù)采集到的壓力值按照設(shè)定的工藝曲線,經(jīng)控制算 法計(jì)算輸出相應(yīng)的數(shù)字與模擬控制信號(hào)完成開(kāi)關(guān)閥與氣動(dòng)薄膜調(diào)節(jié)閥的調(diào)控,壓力檢測(cè)電路 如圖2 所示。

3、調(diào)節(jié)閥控制電路
氣動(dòng)薄膜調(diào)節(jié)閥是通過(guò)調(diào)節(jié)其開(kāi)度來(lái)控制進(jìn)氣量的,對(duì)調(diào)節(jié)閥的準(zhǔn)確快速控制是對(duì)鑄罐 內(nèi)部壓力控制的關(guān)鍵,這也是直接影響鑄件質(zhì)量的重要因素,控制軟件通過(guò)PCI-1716 數(shù)據(jù) 采集卡的16 位D/A 模塊輸出端輸出0~5V 電壓經(jīng)V/I 隔離轉(zhuǎn)換模塊ISO-U1-P1-O1 轉(zhuǎn)換成 4~20mA 的電流信號(hào)來(lái)完成氣動(dòng)薄膜調(diào)節(jié)閥開(kāi)度的控制。控制系統(tǒng)具有兩路調(diào)節(jié)閥控制電 路,分別實(shí)現(xiàn)對(duì)上、下鑄罐進(jìn)氣量的控制。調(diào)節(jié)閥控制電路如圖3 所示。
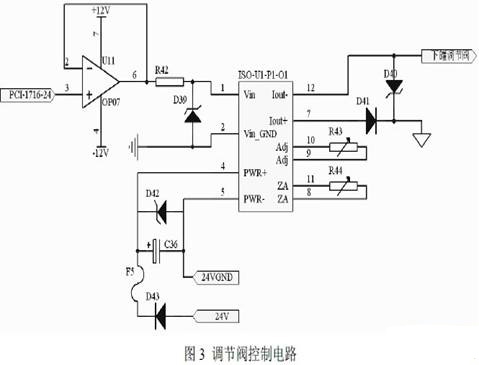
4、軟件結(jié)構(gòu)
控制軟件是真空差壓鑄造控制系統(tǒng)的關(guān)鍵,對(duì) PCI-1716 控制和先進(jìn)智能控制算法的程 序?qū)崿F(xiàn)又是控制軟件的核心技術(shù)。本設(shè)計(jì)采用面向?qū)ο蟮母呒?jí)C++語(yǔ)言,在Visual C++6.0 下進(jìn)行控制軟件程序的代碼編輯、編譯、調(diào)試等工作。軟件結(jié)構(gòu)如圖4 所示。
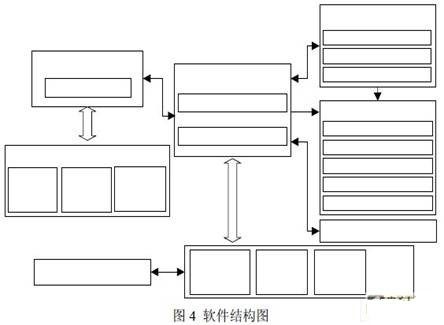
(1)硬件管理模塊:管理PCI-1716 數(shù)據(jù)采集卡及驅(qū)動(dòng)程序,是連接控制軟件與被控對(duì)象的 橋梁。本模塊將PCI-1716 板卡驅(qū)動(dòng)程序及數(shù)據(jù)結(jié)構(gòu)封裝成了CCardCtrl 類,在對(duì)板卡管理之前必須添加必要的庫(kù)文件。首先安裝研華設(shè)備管理器,然后在創(chuàng)建的VC++工程中添加 driver.h 頭文件和adsapi32.lib 設(shè)備驅(qū)動(dòng)庫(kù)。
(2)人機(jī)交互模塊:主要完成工藝參數(shù)設(shè)置,顯示鑄造設(shè)備運(yùn)行狀態(tài)、所有參數(shù)信息,并 完成以下功能:在設(shè)置窗口設(shè)置工藝參數(shù)和修改管理員密碼;在流程和實(shí)時(shí)數(shù)據(jù)顯示窗口顯 示各測(cè)點(diǎn)的實(shí)時(shí)數(shù)據(jù);在跟蹤曲線窗口實(shí)時(shí)繪制上下鑄罐的壓力走勢(shì)圖;在報(bào)警窗口顯示報(bào) 警信息。
(3)數(shù)據(jù)管理模塊:定時(shí)存儲(chǔ)鑄造數(shù)據(jù),即時(shí)完成表格、曲線等形式數(shù)據(jù)的打印等。該模塊采用數(shù)據(jù)庫(kù)技術(shù),設(shè)計(jì)了CData 類來(lái)管理鑄造數(shù)據(jù),用數(shù)據(jù)文件的形式備份數(shù)據(jù)。設(shè)計(jì) 了CADOconn 類運(yùn)用ADO 接口技術(shù)連接SQL Server 2000 數(shù)據(jù)庫(kù)管理系統(tǒng)作為數(shù)據(jù)管理工 具。為了方便調(diào)用,提高程序運(yùn)行效率,將采集的壓力數(shù)據(jù)、閥門的處理數(shù)據(jù)和工步等信息 數(shù)據(jù)采用MFC 中已有的數(shù)據(jù)存儲(chǔ)結(jié)構(gòu),方便快捷的處理數(shù)據(jù)。為了數(shù)據(jù)類型安全,防止內(nèi) 存泄露,選擇template 版本定義如下::CTypedPtrArray data。
(4)控制模塊:該模塊是整個(gè)控制系統(tǒng)的核心,為了提高程序的執(zhí)行效率,本設(shè)計(jì)采用了 多線程技術(shù)將定時(shí)采集控制與監(jiān)控界面定時(shí)刷新分別放在兩個(gè)線程。實(shí)時(shí)數(shù)據(jù)采集模塊采用 Windows 多媒體定時(shí)器TimeSetEvent()函數(shù),該函數(shù)定時(shí)精度可達(dá)1ms,將定時(shí)采樣、工藝 控制定義在lpFunction 回調(diào)函數(shù)中,本系統(tǒng)采樣間隔為50ms。另外,在定時(shí)器使用完畢后, 應(yīng)及時(shí)調(diào)用TimeKillEvent()將之釋放。工藝運(yùn)行模塊是控制模塊的核心,它執(zhí)行的精確與否 將直接影響鑄件的質(zhì)量。工藝運(yùn)行模塊根據(jù)采集到的壓力值按照設(shè)定的工藝曲線,通過(guò)控制 算法計(jì)算出相應(yīng)的數(shù)字與模擬控制數(shù)據(jù)經(jīng)硬件管理模塊完成開(kāi)關(guān)閥與氣動(dòng)薄膜調(diào)節(jié)閥的精 確調(diào)控。
5、結(jié)論
硬件上 4 路壓力檢測(cè)電路和2 路調(diào)節(jié)閥控制電路達(dá)到了極高的線性度(非線性度<2%)。 壓力測(cè)量范圍為0~1.0MPa,測(cè)量分辨率15.0Pa;輸出模擬量精度在±0.1%。軟件上提供了 快捷的工藝參數(shù)設(shè)置,直觀的實(shí)時(shí)壓力數(shù)據(jù)、壓力曲線和工藝進(jìn)程跟蹤,方便的歷史數(shù)據(jù)記 錄查詢和靈活的聲光電報(bào)警等功能。圖5 為真空度24KPa、充型和保壓壓差40KPa、充型延 時(shí)10 秒、保壓壓力250KPa、保壓時(shí)間40 秒的工藝參數(shù)模擬運(yùn)行曲線。實(shí)驗(yàn)證明整個(gè)控制 系統(tǒng)運(yùn)行穩(wěn)定、人機(jī)交互性強(qiáng)、響應(yīng)速度快、控制精度高、基本達(dá)到設(shè)計(jì)要求。
本文作者的創(chuàng)新點(diǎn)是:將 PCI 總線技術(shù)引入到真空差壓鑄造控制系統(tǒng)中,避免了監(jiān)測(cè)與控 制分開(kāi)帶來(lái)的硬件電路設(shè)計(jì)的復(fù)雜性;Visual C++和SQL Server 數(shù)據(jù)庫(kù)技術(shù)的應(yīng)用,使控 制軟件操作簡(jiǎn)單、人機(jī)交互直觀和方便歷史數(shù)據(jù)的分析。
評(píng)論